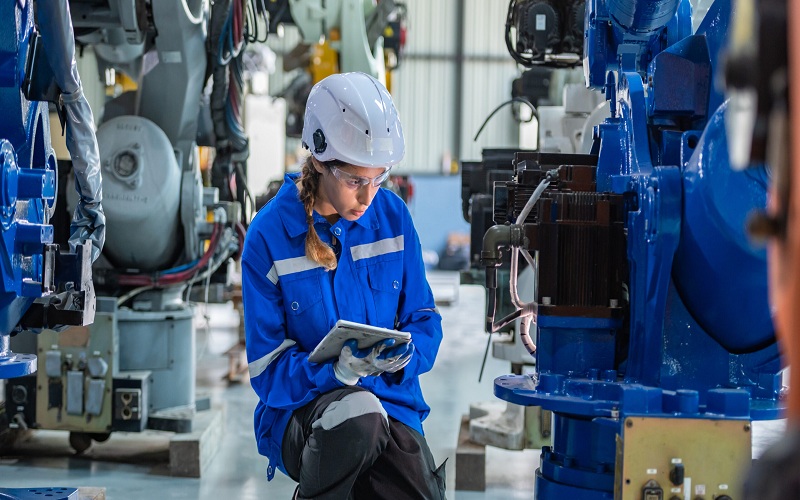
Preventing Downtime: Strategies to Protect Productivity and Customer Trust in Manufacturing
In the complex world of manufacturing, downtime is more than a mere inconvenience—it’s a serious financial threat. When a production line unexpectedly stops, it doesn’t just halt productivity; it depletes resources and undermines the crucial trust manufacturers build with their customers.
The ramifications of downtime extend well beyond operational hiccups. It directly impacts customer relationships by breaking commitments and disappointing clients, who may then look elsewhere for more reliable partners. In a market where timeliness and dependability are critical, any disruption to delivery schedules can be highly damaging.
Although some disruptions are unavoidable, many can be prevented. Common causes of downtime include neglect of preventive maintenance, inadequate employee training, and poor data management. These issues, though they may seem minor initially, can accumulate and lead to severe operational halts.
By investing in preventive maintenance, robust employee training, and efficient data management, manufacturers can shield themselves from the adverse effects of downtime. Proactive measures are essential for maintaining smooth operations and preserving customer trust.
For more detailed strategies on preventing downtime, refer to the accompanying resource. It provides practical advice to help you maintain continuous production and safeguard your manufacturing processes.
The Cost Of Downtime In Manufacturing was created by S Himmelstein and Company, an organization offering any torque transducer to meet your company’s needs.